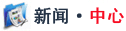
锥齿轮传动装置的优化设计:自20世纪80年代初以来,AC伺服技术得到了迅猛的发展,今天,它已成为精加工设备的首选技术。传动技术也随着伺服技术的发展而进步,市场畅销的传动装置是同轴传动装置,特别是行星齿轮传动装置。
迄今为止,用于伺服技术的锥齿轮传动装置一般是只有一个角度的同轴传动,其实它属于一种有两个传动装置的组合体。这种方式导致在选择和使用锥齿轮传动装置 时,要面对很多的问题。尤其是锥齿轮传动装置的小棘轮问题,因为传动比小、噪声大,所以锥齿轮的传动比只设能到i = 3或4。另外还有费用问题,因为针对某些使用场合必须加设一至两个等级,费用就容易增加了。所以在市场上出现了类似于“锥式行星齿轮减速装置”的标号,这 也就不足为奇了。
另一种传统的锥齿轮传动装置是蜗轮蜗杆传动装置,它虽然可以提供很高的传动比,运行噪声小,但却存在磨损严重、间隙变大、起动效率低、容量和重量大、自阻尼严重等问题。
Alpha Getriebe公司推出的新型HG系列传动装置完全改变了上述的不良现象。这是一种间隙极小的空心轴锥齿轮传动装置,其优点是同一级别上的传动比大、运 行噪声小。事实证明,在3000r/min下所测得的噪声≤62db,同时磨损小,运行效率高。所以,使用这种新型传动装置可以实现稳定的扭转间隙,并且 在各种传动比下都能达到良好的可逆性能。
准双曲面齿轮传动装置本身并不算是技术创新,用在小轿车上的这种传动装置每年多达几百万件。Alpha公司的技术创新是建立在其所开发的用于高精度机器制 造业上的准双曲面齿轮上的。因为高精度机器制造业对齿轮传动的要求不同于小轿车的要求,例如需要用到比较小型的齿轮传动装置,扭转间隙也要求很小。 Alpha公司把汽车上应用成熟的准双曲面技术运用到伺服技术上,自然可以获得良好的利润回报,例如把这种伺服技术运用到附加值的赛车制造业上。
但是纯粹采用减速箱原理并不能解决根本性的问题,对减速箱技术进行优化,本身也要牵涉到部件的精密加工、齿轮参数的优化、FEM整体模仿和精确组装等要求。
转速高,效率也高
准双曲面减速箱可以给用户带来很多好处。转速高和扭矩大的特点可以使机器达到很高的生产效率,由于采用了双曲线技术,新型减速箱的单级传动比可以达到 3:1至10:1,加上扭转间隙小,所以用户可以实现精确的加工作业。在设备的整个使用寿命过程中,扭转间隙可以始终稳定在较低的水平上。尽管功率密度很 大,但是新型减速箱的噪声水平要比普通的减速箱低三倍。
这种新型减速箱适用于所有的伺服技术使用场合,不管是高速的S1作业,还是高动态的S5作业。理想的使用对象有包装设备(纸箱矫直机和纸箱成型机、包纸 机、装袋机等)、装/卸载机器人、码垛机、工业机器人的7号和8号轴以及打印机和木材、玻璃和石料行业用的平底加工设备。
新型锥齿轮减速箱装置共有五种型号,最大加速扭矩可以达到640Nm,扭转间隙<4角分(测量力矩为加速力矩),同Alpha公司其他锥齿轮减速箱 一样,要在出厂前接受百分之百的检验。因为减速箱在实际工作中基本不会发生磨损,所以不仅可以实现免维护,而且在整个使用寿命中还可以保持稳定的扭转间 隙,达到高精度的目标。锥齿轮减速箱在出厂前已经经过润滑,只需在各个装配点上加一点润滑油,用户可以省去按期的维护工作。
额定转速为3000 r/min以上,最大转速可达6000r/min,大转速加上大扭矩,即可极大地提高快速包装机、装/卸载机器人和其他多种工作场合的效率。
新型锥齿轮减速箱的可靠性和灵活性
HG减速箱是世界上唯一能够与de-facto标准相兼容的空心轴减速箱,传动装置由一个带有收缩盘连接件和普通法兰的长的Alpha空心轴构成,在驱动 部里设有Alpha通用型电机装置,它与现有的Alpha锥齿轮减速箱装置完全兼容,同时也符合使用更大电机轴径的发展趋势。使用Alpha公司的 Cymex 3设计软件,可以实现简便的设计和对减速箱和电机的选型。
除了可靠性好的特点之外,锥齿轮减速箱装置同时也拥有良好的灵活性。减速箱与电机的匹配也可以非常简单,它可以与所有的伺服电机相匹配,实践证明拥有专利技术的Alpha通用型匹配装置可以做到这一点。由于结构紧凑、结实耐用,所以在设计上可以达到较大的灵活度。
以用户眼光看来,产品质量最重要。由于Alpha减速箱要经历24小时的出厂连续检验,所以可以达到可靠和快速的使用目的。